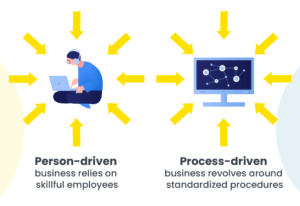
Process-Driven Systems
- Efficiency and Consistency: Process-driven systems emphasize standardization and automation. They rely on predefined procedures and workflows to streamline production processes. This approach can lead to high levels of efficiency and consistency in output, reducing the margin for error.
- Reduced Labor Costs: By automating repetitive tasks and minimizing human intervention, process-driven systems often result in lower labor costs. This can be particularly beneficial for large-scale manufacturing operations.
- Scalability: Process-driven systems are typically easier to scale up or down in response to changes in demand. Automated machinery can be adjusted to meet varying production requirements, making it an attractive option for companies with fluctuating workloads.
- Quality Control: These systems often incorporate quality control measures, such as sensors and inspection devices, to ensure that products meet stringent standards. This helps in maintaining high product quality and reducing defects.
- Data Analytics: Process-driven systems generate vast amounts of data, which can be leveraged for continuous improvement. By analyzing this data, manufacturers can identify bottlenecks, optimize processes, and make data-driven decisions.
People-Driven Systems
- Flexibility and Adaptability: People-driven systems place a strong emphasis on human expertise and adaptability. Skilled workers can quickly adjust to changing production needs and respond to unexpected challenges.
- Complex or Customized Products: When manufacturing complex or highly customized products, human workers can provide the necessary craftsmanship, attention to detail, and problem-solving abilities that machines may lack.
- Innovation and Creativity: Human workers can contribute to innovation and process improvement by offering insights and ideas based on their experience. They can adapt to unique situations and find creative solutions to problems.
- Employee Satisfaction: Fostering a work environment that values the contributions of skilled workers can lead to higher job satisfaction and morale among employees, which, in turn, can positively impact overall productivity.
- Lower Initial Investment: Implementing people-driven systems may require less initial capital investment compared to heavily automated processes. This can be advantageous for smaller manufacturers or those with limited resources.
Choosing the Right Balance
In reality, most manufacturing companies do not need to choose between exclusively process-driven or people-driven systems. A successful approach often involves finding the right balance between these two paradigms. This means leveraging automation and technology where it makes sense, while also recognizing the value of human skills and expertise.
Here are some considerations for finding the right balance:
- Evaluate Your Product: Consider the nature of your product. Is it highly standardized and suitable for automation, or does it require human craftsmanship and customization?
- Demand Variability: Analyze your demand patterns. If your production needs fluctuate frequently, a more flexible people-driven approach may be necessary.
- Technology Integration: Explore opportunities to integrate automation and technology into your processes without sacrificing the advantages of human input.
- Training and Skill Development: Invest in the training and skill development of your workforce to ensure they can adapt to changing technologies and processes.
- Continuous Improvement: Regardless of your approach, prioritize continuous improvement. Collect and analyze data to identify areas where automation or human intervention can drive better results.
The choice between process-driven and people-driven systems in manufacturing industries is not a binary decision. Successful manufacturing companies often find a way to combine the advantages of both approaches to maximize efficiency, quality, and adaptability. The key lies in understanding the specific needs of your product, your workforce, and your market. By striking the right balance between automation and human expertise, manufacturers can thrive in today’s rapidly evolving industrial landscape.
We manufacture machined components as per customer requirements. More Info >> Check here.