In the intricate world of machining, where precision is paramount, the drill angle becomes a critical factor in ensuring accuracy and efficiency during drilling operations. This often-overlooked aspect plays a pivotal role in determining the success of the operation and the quality of the machined components produced. Let’s delve into the importance of drill angle and how it influences the drilling process on machined components.
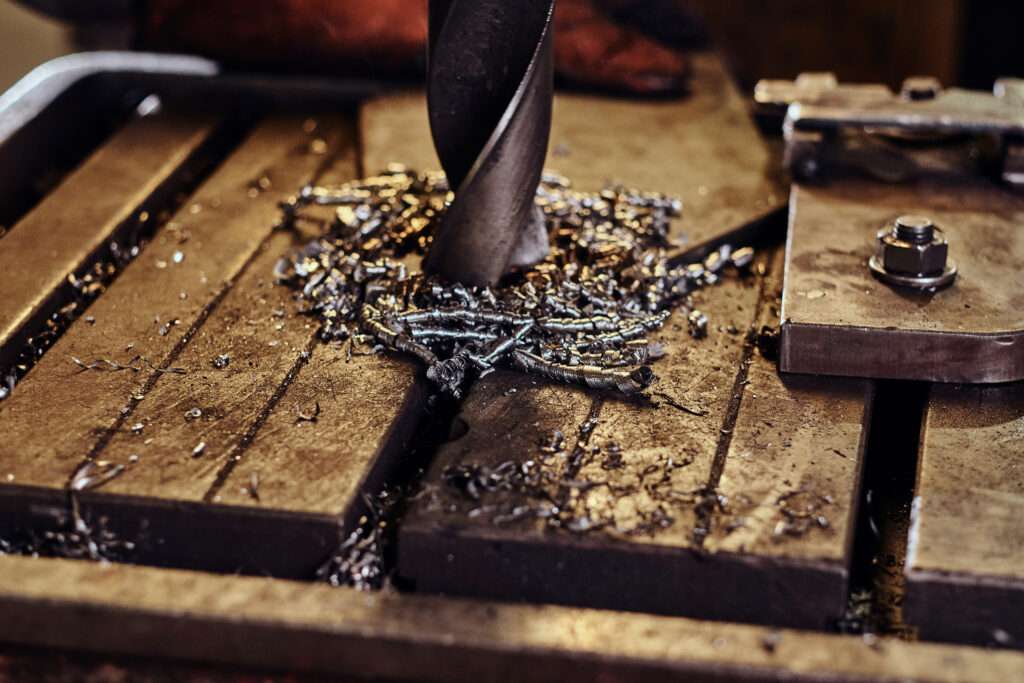
Understanding Drill Angle: The Basics
The drill angle, also known as the point angle or the included angle, refers to the angle formed between the two cutting edges of the drill bit. This seemingly minor detail holds immense significance in drilling operations, impacting the tool’s performance, chip formation, and the overall quality of the machined holes.
Precision in Action: Drill Angle and Accuracy
One of the primary considerations in machining is achieving precision, and the drill angle directly influences the accuracy of the drilled holes. The selection of an appropriate drill angle ensures that the tool engages with the workpiece in a controlled manner, preventing issues such as deflection, wandering, or deviation from the desired path. This precision is especially crucial in industries like aerospace and medical devices, where tight tolerances are non-negotiable.
Chip Formation: Efficiency in Machining
Efficient chip formation is a key aspect of drilling operations, and the drill angle plays a crucial role in determining how chips are formed and evacuated. The right drill angle facilitates the creation of manageable and well-formed chips, preventing chip congestion, tool jamming, and ensuring a smooth drilling process. This efficiency not only improves the drilling operation’s speed but also enhances the overall lifespan of the cutting tool.
Tool Life and Wear: Impact of Drill Angle
The drill angle has a direct impact on the tool’s wear and, consequently, its lifespan. An improper drill angle can lead to accelerated wear, overheating, and premature tool failure. By selecting the right drill angle, machinists can optimize tool life, reducing the frequency of tool changes and minimizing downtime in production.
Material Matters: Drill Angle and Workpiece Material Compatibility
Different materials require different approaches, and the drill angle is no exception. The choice of drill angle should consider the workpiece material to ensure efficient material removal and hole formation. Whether dealing with metals, plastics, or composites, the drill angle must be aligned with the material properties for optimal results.
Strategies for Success: Selecting the Right Drill Angle
The optimal drill angle is influenced by factors such as workpiece material, cutting speed, feed rate, and the specific requirements of the drilling operation. Machinists must carefully consider these factors to select the right drill angle, balancing the need for precision with efficiency.
Conclusion: Elevating Drilling Operations with the Right Drill Angle
In conclusion, the drill angle is a subtle yet influential factor in the world of machining. Its impact on accuracy, chip formation, tool life, and material compatibility makes it a crucial consideration for machinists aiming for excellence. By understanding the importance of drill angle and implementing the right strategies, machinists can elevate drilling operations, ensuring the production of high-quality machined components that meet the most demanding specifications.
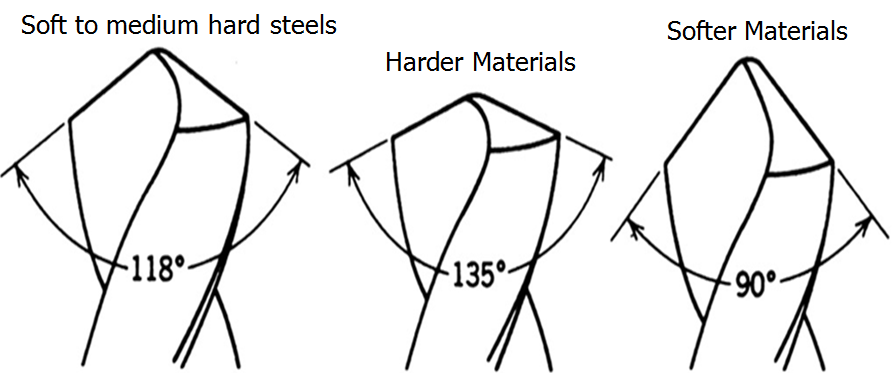