In the world of plastic injection molding, precision and durability are everything. Whether it’s for automotive components, consumer electronics, or industrial assemblies, ensuring strong and reliable connections between plastic parts and other materials is crucial. This is where threaded and non-threaded metal inserts—especially steel and brass molding inserts—play a game-changing role.
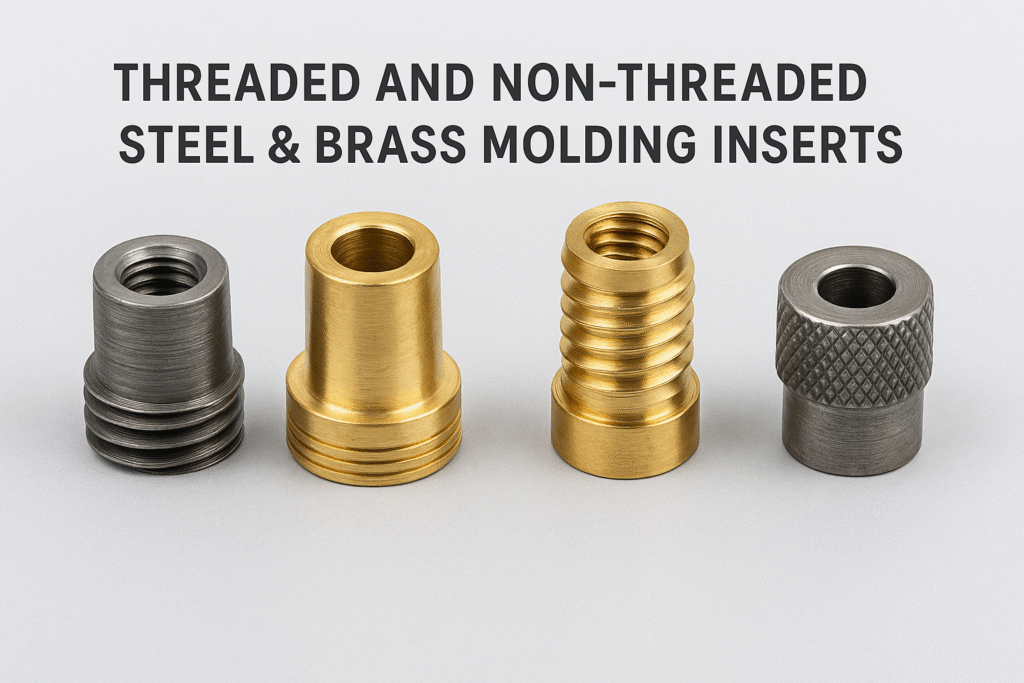
What Are Molding Inserts?
Molding inserts are metal components embedded into plastic parts during or after the injection molding process. These inserts provide secure fastening points, load-bearing capabilities, and increased wear resistance for plastic components.
They are commonly categorized into:
Threaded Inserts: Allow screws or bolts to be securely fastened.
Non-Threaded Inserts: Serve as bushings, alignment guides, or reinforcement features without internal threads.
Threaded Inserts: Strength Meets Versatility
Threaded steel or brass inserts are used when a plastic component requires repeated assembly/disassembly or where a high-strength fastening point is needed.
Common Applications:
Electrical enclosures
Automotive dashboards
Consumer appliances
Aerospace control panels
Benefits of Threaded Inserts:
Strong threads in weak materials: Plastic alone can’t hold screws under repeated stress, but metal inserts solve this problem.
Corrosion resistance: Especially in brass, which resists oxidation and moisture.
Thermal resistance: Ideal for parts exposed to heat or thermal cycling.
Reusable threads: Threads don’t wear out easily with repeated use.
Non-Threaded Inserts: Simple, but Essential
Non-threaded inserts may seem less glamorous, but they are vital for guiding, reinforcing, and aligning plastic parts. These inserts are often used as:
Locating pins
Pivot points
Axial supports
Bushings for shafts or dowels
Materials & Advantages:
Steel Inserts: Preferred for high-stress or load-bearing applications due to their strength and rigidity.
Brass Inserts: Chosen for ease of machining, anti-corrosive properties, and good conductivity (where needed).
Why Use Steel and Brass?
Choosing between steel and brass depends on your specific application:
Property | Steel Inserts | Brass Inserts |
---|---|---|
Strength | Very High | Moderate |
Corrosion Resistance | Requires coating | Naturally corrosion-resistant |
Machinability | Lower | Excellent |
Cost | Lower | Higher |
Thermal Conductivity | Low | High |
Installation Methods
Inserts can be installed via:
Mold-In: Insert placed in mold before injection. Ideal for strong bonds and part integrity.
Ultrasonic Insertion: Post-molding, heat generated by ultrasonic vibrations melts plastic around the insert.
Heat Staking: Direct heat melts the plastic and allows the insert to be pressed in.
Press-Fit: For non-threaded inserts or temporary applications.
Why It Matters in Product Design
Inserts aren’t just add-ons; they’re critical engineering elements. Using the right type of insert:
Improves assembly reliability
Extends the life of plastic components
Enables modular design and easier repairs
Supports metal-to-plastic transitions in hybrid assemblies
Precision Inserts from Mech Source
At Mech Source, we manufacture custom threaded and non-threaded brass and steel inserts to your exact specifications. Whether you’re producing millions of molded parts or developing a high-precision prototype, our inserts are:
Manufactured with tight tolerances
Available in standard or custom geometries
Delivered with on-time precision
Backed by quality control and expert support
Let’s Build Stronger Connections
Looking for a reliable supplier of precision brass and steel molding inserts for plastic injection applications?
Mech Source delivers performance, precision, and peace of mind—one insert at a time.
📩 Contact us today to get a quote or consult with our experts on your insert molding needs.