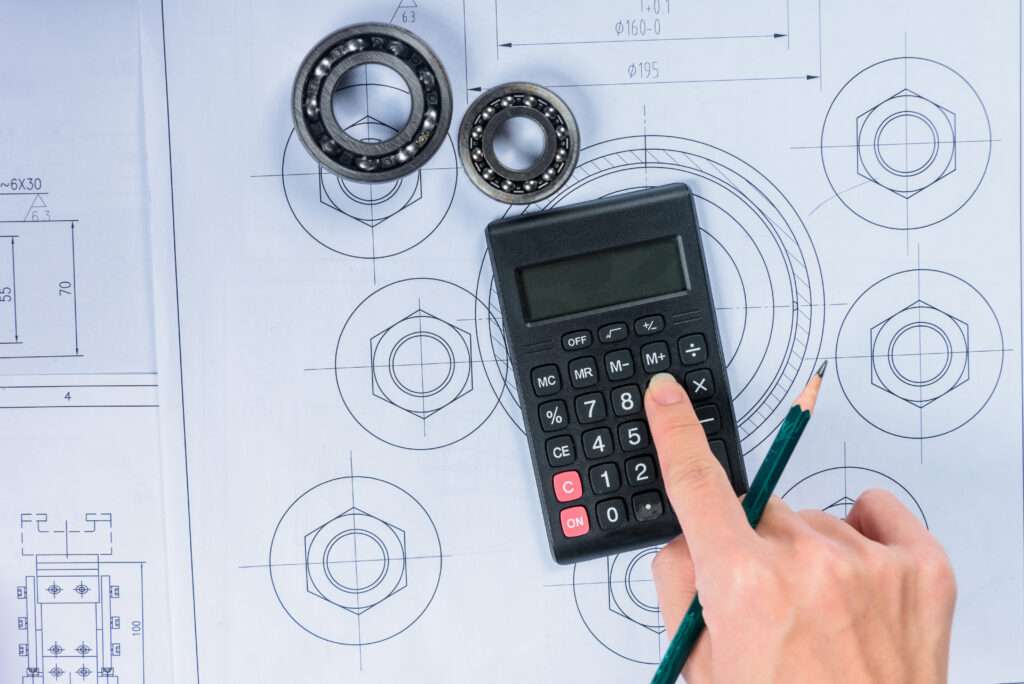
The costing of machined components involves a detailed analysis of various factors to determine the overall production cost. Here are the key elements considered in working out the cost of machined components:
Material Costs:
-
- Raw Materials: The cost of the raw materials used in machining, including metals, plastics, or other materials, is a fundamental component of the overall cost.
- Scrap and Waste: Factoring in the potential waste or scrap generated during the machining process is essential for accurate costing.
Labor Costs:
-
- Machinist Wages: The labor costs associated with the machinists who operate the CNC machines or perform manual machining processes.
- Setup Time: The time required for setting up the machines and preparing them for the specific machining operation.
Machine Costs:
-
- Depreciation: Calculating the depreciation of the machining equipment over its useful life.
- Maintenance: Regular maintenance costs to ensure the machines operate efficiently.
- Tooling Costs: The cost of tooling, including cutting tools, inserts, and other tooling components.
Overhead Costs:
-
- Utilities: Including electricity, water, and other utility costs associated with running the machining equipment.
- Rent/Lease: The cost of the facility where the machining operations take place.
- Insurance: Insurance costs for the facility, equipment, and personnel.
Quality Control Costs:
-
- Inspection and Testing: The cost of inspecting and testing machined components to ensure they meet quality standards.
- Quality Assurance Personnel: The cost of personnel responsible for maintaining quality standards.
Programming Costs:
-
- CNC Programming: For components produced using CNC machining, the cost associated with creating and optimizing the CNC programs.
Packaging and Shipping:
-
- Packaging Materials: The cost of materials used for packaging finished machined components.
- Shipping Costs: The cost of transporting the components to the customer.
Volume and Batch Size:
-
- Economies of Scale: The cost per unit may vary based on the volume of production. Larger production runs often result in lower per-unit costs due to economies of scale.
Lead Time and Urgency:
-
- Rush Order Costs: If a customer requires a rushed or expedited production, additional costs associated with overtime and expedited shipping may be factored in.
Markup for Profit:
-
- Profit Margin: A markup is applied to the total cost to cover profit and contribute to the financial sustainability of the machining business.
It’s important to note that the costing process may vary based on the specific machining methods employed (e.g., CNC machining, manual machining) and the complexity of the components. Additionally, businesses often use specialized costing software or enterprise resource planning (ERP) systems to streamline and automate the costing process.
Accurate costing is crucial for competitive pricing, ensuring profitability, and making informed business decisions. Regular review and adjustment of costing methods based on changing market conditions and production efficiencies are also key practices in the manufacturing industry.
Let me know if there is anything more you consider while costing in your organisation.